Quality Control vs Quality Assurance: What’s The Difference?
Quality Control vs Quality Assurance represents a comparison between two fundamental aspects of quality management in any production or service industry. Quality Control (QC) is primarily focused on the identification and rectification of defects in the final product. It is a reactive approach, where the emphasis is on inspection and testing of products to ensure they meet the established standards of quality. QC is about ensuring that the output meets specific quality criteria and often involves various testing and validation procedures.
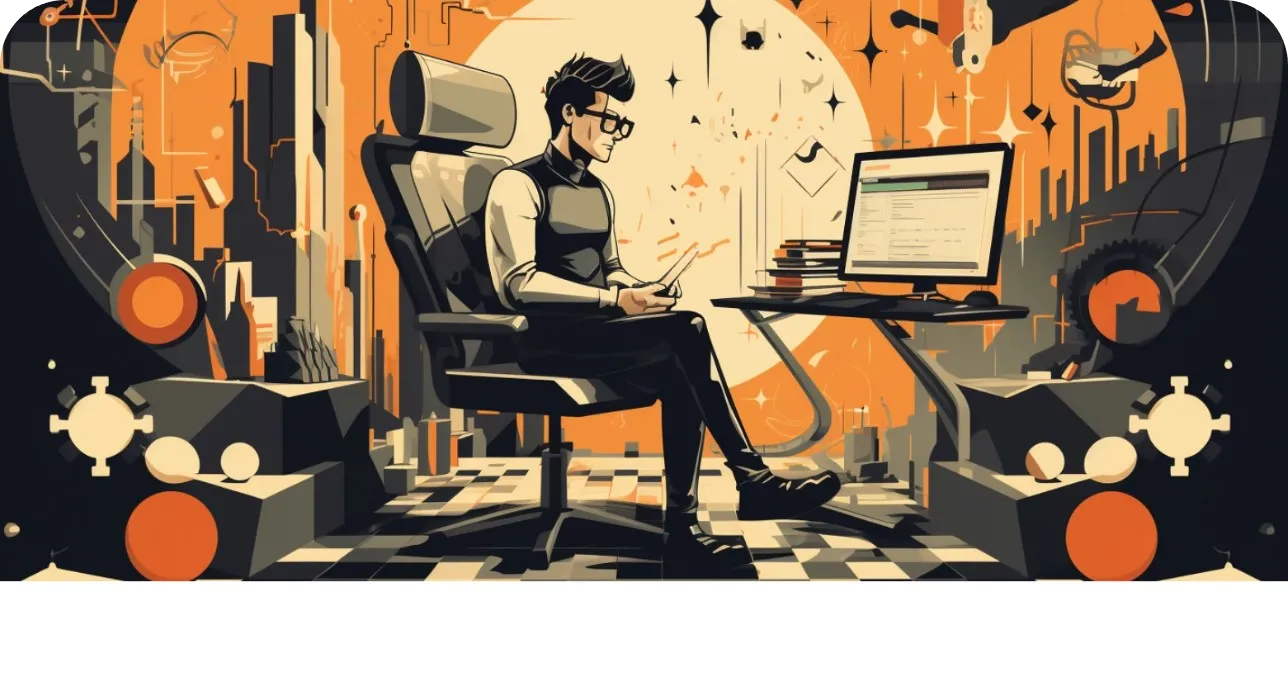
Table of content
Table of Contents
We’re on board to help with your product. Don’t hesitate to get in touch.
Contact Us Let’sTalk
Quality Control vs Quality Assurance represents a comparison between two fundamental aspects of quality management in any production or service industry. Quality Control (QC) is primarily focused on the identification and rectification of defects in the final product. It is a reactive approach, where the emphasis is on inspection and testing of products to ensure they meet the established standards of quality. QC is about ensuring that the output meets specific quality criteria and often involves various testing and validation procedures.
On the other hand, Quality Assurance (QA) is a proactive process aimed at preventing defects before they occur. This approach focuses on the processes and procedures that lead to the creation of the final product. QA involves the systematic planning and execution of various activities to ensure that the processes are adequate to produce a product of the desired quality. It’s more about process control, ensuring that every step in the production process is designed and operated in a manner that mitigates the risk of defects.
In essence, while Quality Control is a product-oriented process concerned with the output, Quality Assurance is a process-oriented approach focused on the prevention of flaws in the design, production, and development phases. Both are critical for ensuring the overall quality of products and services, but they operate at different stages and scopes within the quality management spectrum.
Quality control vs quality assurance: What’s the difference
Quality Control and Quality Assurance are two different organizational practices, yet both are critical to a successful business. However, the two practices differ in key areas such as, goals, target audiences, metrics, and how you track them. As such, they are not interchangeable.Generally speaking, Quality Control (QC) is the process of monitoring and measuring the quality of a product or service to ensure it meets predetermined standards. QC is used at the point of production, meaning it occurs after the product has left the assembly line.
The goal of QC is to find any defects in the product. In this, QC checks that the correct materials have been used, and that the production process meets the standards required for the product. QC uses control charts to help visualize data and track quality metrics.
Quality Assurance (QA) is an organization’s system for ensuring the finished product meets its production standards. The QA process, however, generally begins before the production process begins. QA audits the production process to ensure it meets the standards required to turn raw materials into usable products.
The goal of QA is to find any gaps in the production process. In this, QA audits the process to ensure the correct materials have been selected, the production team meets the required skill set, and that the production process meets the standards required for the product.

Why is QA Important?
Quality assurance is important because it helps you deliver consistent products and services to your customers. Without adequate quality assurance practices in place, you risk delivering products that fall below your customers’ expectations. This could lead to lost customers and reduced revenue.
Most businesses strive to put their best foot forward, but they are also subject to the human factor. Even the most careful and skilled business owners can miss something, especially when it comes to processes that happen behind the scenes. As such, quality assurance processes help mitigate the risk of delivering products or services that do not live up to your customers’ expectations.
When Should You Use QA?
You should use quality assurance when you’re not certain whether or not the product or service meets your standards. In this case, you need to verify that the production process meets your requirements before you begin selling your goods.One example of when you might use quality assurance is when you’re developing a new product. You want to test the product against the quality standards you’ve set and make sure any design flaws are smoothed out before you start selling the product.Another example is when you’re bringing a new supplier online. You want to track the production of your product to make sure it meets your quality standards.
When Should You Use QC?
You should use quality control when you’ve verified that the product or service meets your standards. In this case, you want to examine whether or not the production process continues meeting your standards.
One example of when you might use quality control is when you’ve hired new employees. You want to make sure they’re producing the same quality of product as your other employees.Another example is if you’ve changed suppliers. You want to track the production of your product to make sure it meets your quality standards.
Quality control vs quality assurance: final words
When it comes to business operations, it’s important to know the difference between quality control and quality assurance. Quality control occurs after the product has been produced. QC checks that the correct materials have been used and that the production process meets the standards required for the product.
One example of when you might use quality assurance is when you’re developing a new product. You want to make sure the product meets your quality standards before you start selling it. Another example is when you’re bringing a new supplier online. You want to track the production of your product to make sure it meets your quality standards.
Ultimately, QC and QA are two distinct processes that are critical to any successful business. With that in mind, you should use both QA and QC processes to make sure your product meets quality standards.